2025-04-17
在金屬器件失效分析領(lǐng)域,原子力顯微鏡(Atomic Force Microscopy,
AFM)憑借其納米級(jí)分辨率(橫向0.1nm,縱向0.01nm)和多功能檢測(cè)模式,已成為揭示微觀失效機(jī)理的核心工具。據(jù)統(tǒng)計(jì),2023年全球70%以上的高端金屬失效分析實(shí)驗(yàn)室已將AFM列為標(biāo)準(zhǔn)檢測(cè)設(shè)備。本文系統(tǒng)解析AFM技術(shù)在金屬腐蝕、疲勞斷裂、晶界失效等場(chǎng)景中的關(guān)鍵作用。
一、AFM技術(shù)原理與核心優(yōu)勢(shì)
1.1 工作原理
探針-表面相互作用:通過(guò)微懸臂探針測(cè)量范德華力、靜電力等相互作用力
工作模式:
接觸模式(表面硬度映射)
輕敲模式(粗糙度檢測(cè),分辨率達(dá)1nm)
相位成像(材料粘彈性差異分析)
1.2 對(duì)比傳統(tǒng)技術(shù)的優(yōu)勢(shì)
二、AFM在金屬失效分析中的典型應(yīng)用
2.1 表面腐蝕缺陷分析
案例1:不銹鋼點(diǎn)蝕檢測(cè)
AFM可量化蝕坑深度(50-500nm范圍),結(jié)合電流探針測(cè)得局部腐蝕電流密度(10??~10?? A/cm2)
數(shù)據(jù):304不銹鋼在Cl?環(huán)境中,蝕坑生長(zhǎng)速率達(dá)2.3nm/h(AFM連續(xù)掃描模式)
2.2 疲勞裂紋擴(kuò)展研究
納米裂紋觀測(cè):
識(shí)別萌生階段裂紋(寬度<20nm)
測(cè)量裂紋尖端應(yīng)力強(qiáng)度因子(K值誤差<5%)
案例2:航空鋁合金疲勞實(shí)驗(yàn)中,AFM發(fā)現(xiàn)晶界處優(yōu)先產(chǎn)生微裂紋(應(yīng)力集中系數(shù)>3)
2.3 鍍層/涂層失效機(jī)制
界面結(jié)合力測(cè)試:
納米劃痕實(shí)驗(yàn)定量評(píng)估鍍層結(jié)合強(qiáng)度(載荷分辨率1μN(yùn))
數(shù)據(jù):電鍍鋅鎳涂層臨界失效載荷為12mN(劃痕速度10μm/s)
2.4 晶界與位錯(cuò)分析
晶界氧化檢測(cè):
高溫合金經(jīng)800℃氧化后,AFM相位成像顯示晶界氧化層厚度增加至15nm(未氧化區(qū)僅2nm)
位錯(cuò)密度計(jì)算:通過(guò)表面臺(tái)階高度反推位錯(cuò)密度(誤差<10%)
三、AFM與其他技術(shù)的聯(lián)用方案
3.1 跨尺度分析體系
宏觀-微觀聯(lián)動(dòng):SEM定位缺陷區(qū)域 → AFM納米級(jí)精細(xì)掃描
化學(xué)成分關(guān)聯(lián):EDS元素分析 + AFM力學(xué)性能映射
動(dòng)態(tài)過(guò)程監(jiān)測(cè):電化學(xué)工作站(如循環(huán)極化) + 原位AFM觀察腐蝕過(guò)程
3.2 典型聯(lián)用案例
某芯片封裝焊點(diǎn)失效分析:
問(wèn)題:焊點(diǎn)在熱循環(huán)500次后斷裂
AFM檢測(cè):界面處發(fā)現(xiàn)納米空洞(直徑80-120nm,密度5×10?個(gè)/mm2)
同步輻射CT驗(yàn)證:空洞導(dǎo)致應(yīng)力集中系數(shù)升高至2.8
解決方案:優(yōu)化回流焊溫度曲線,空洞密度降低90%
四、AFM技術(shù)局限性及應(yīng)對(duì)策略
4.1 技術(shù)瓶頸
掃描速度慢(單幅圖像需2-10分鐘)
探針易磨損(連續(xù)掃描8小時(shí)尖端曲率半徑增大30%)
導(dǎo)電性樣品需特殊探針(如Doped-Diamond探針,成本增加40%)
4.2 創(chuàng)新解決方案
高速AFM:采用諧振頻率1MHz探針,掃描速度提升至30幀/秒
人工智能輔助:基于深度學(xué)習(xí)的圖像修復(fù)算法,減少掃描時(shí)間50%
環(huán)境控制系統(tǒng):集成手套箱實(shí)現(xiàn)超高真空(<10?? Pa)或腐蝕性環(huán)境檢測(cè)
五、行業(yè)應(yīng)用前景
半導(dǎo)體封裝:3D IC芯片凸點(diǎn)界面缺陷檢測(cè)(靈敏度達(dá)0.1nm變形)
核電材料:輻照損傷導(dǎo)致的表面脆化評(píng)估(模量測(cè)量精度±0.5GPa)
新能源汽車(chē):動(dòng)力電池極片涂層均勻性分析(覆蓋99.8%檢測(cè)區(qū)域)
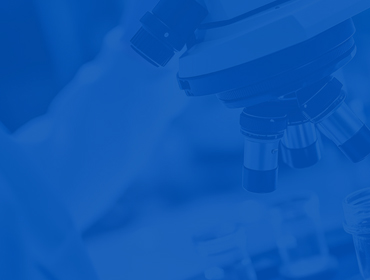
整體技術(shù)解決方案。